Diamond setters are highly skilled artisans who play a crucial role in the jewellery industry by securely mounting diamonds and gemstones into various pieces.
At Solid Gold Diamonds, we have the largest workshop in Perth Western Australia, and arguably in Australia.
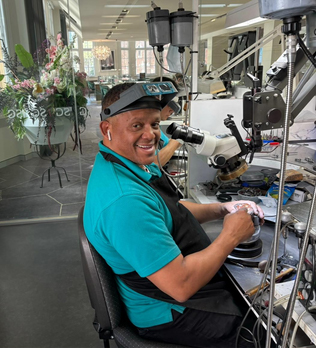
We recently sat down with Vincent, one of our seasoned diamond setters with over 35 years of experience to gain insights into his craft.
Vincent’s expertise in diamond setting is unparalleled, ensuring each precious stone is meticulously places to enhance its brilliance and security. Precision and fine craftsmanship shines throughout the diamond setter team as they work on various jewellery for clients worldwide.
Curious to learn more about the artistry behind diamond setting? Read on as Vincent shared his journey, techniques and the importance of being versatile in your skillset in a jewellery manufacturing workshop.
What training or apprenticeship did you undergo to become a skilled diamond setter? How long did it take to master the craft?
The apprenticeship takes 5 to 7 years, which I completed in Cape Town South Africa, followed by a trade test. As the setter, setting the diamond or gemstone is one of the last procedures in creating a jewellery piece. It is advantageous to know all the other processes involved in the creation of an item of jewellery, knowing this helps in preparing to set the diamond or gemstone, it adds to your skill, knowledge and understanding.
Are there many different diamond and gemstone setting techniques you have to be skilled in ?
There are many different techniques, for example, prong, bezel, pave, channel. They all have their different challenges and take years to master the various skills required for each technique. The type of diamond shape can be challenging with princess cut diamonds, for example, among the shapes that require experience and expertise. Various gemstones also require skill because of their unique characteristics with emerald and opal being the most challenging.
What tools and equipment are essential for a diamond setter’s work?
There are many very specialised tools, different types of settings require specific tools. The drill, setting bur, bezel pusher, prong pusher, burnisher, microscope, ring clamps. You have to be skilled and expert across a full range of specialised equipment.
In your experience, what is the most rewarding aspect of being a diamond setter?
Being creative, being able to create something of real beauty. Working in a team of creative people where there is real passion for the work we do. I think it important to pass these skills onto the next generation, so the art of diamond setting is not lost.
What is a memorable item of jewellery that you helped create that makes you proud?
Being involved and part of a team making a brooch for Queen Elizabeth, while in South Africa, was very challenging, but a very proud moment for me.
What advice would you give to someone interested in pursuing a career as a diamond setter?
There are some great courses at Tafe, but finding a jewellery manufacturing workshop to train in is essential, where you can learn from experienced and expert setters. You have to be teachable and ask questions. Being in a workshop where you can learn all aspects of jewellery manufacturing from skilled artisans is the best route to take.
Thank you Vincent.